Revision as of 20:19, 23 January 2008 editVersageek (talk | contribs)Edit filter managers, Autopatrolled, Checkusers, Administrators38,588 editsm Reverted 3 edits by 82.136.75.48.← Previous edit | Revision as of 19:16, 24 January 2008 edit undo82.136.117.133 (talk) →ReferencesNext edit → | ||
Line 57: | Line 57: | ||
* Pyzdek, T, "Quality Engineering Handbook", 2003, ISBN 0824746147 | * Pyzdek, T, "Quality Engineering Handbook", 2003, ISBN 0824746147 | ||
* Godfrey, A. B., "Juran's Quality Handbook", 1999, ISBN 007034003 | * Godfrey, A. B., "Juran's Quality Handbook", 1999, ISBN 007034003 | ||
* Process Assessment and Improvement ISBN 0-387-23182-X | * Process Assessment and Improvement ISBN 0-387-23182-X | ||
] | ] | ||
Revision as of 19:16, 24 January 2008
Quality management is a method for ensuring that all the activities necessary to design, develop and implement a product or service are effective and efficient with respect to the system and its performance.
W. Edwards Deming is best known for his management philosophy establishing quality, productivity, and competitive position. He has formulated 14 points of attention for managers, some of these points are more appropriate for service management:
- Break down barriers between departments
- Management should learn their responsibilities, and take on leadership
- Improve constantly
- Institute a programme of education and self-improvement
Quality improvement
The following diagram is the Shewhart cycle (PDCA) for quality improvements, made popular by Deming.
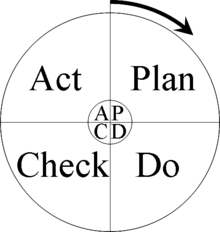
The philosophy is to keep improving the quality of an organization. It is defined by four keys:
- Plan: Design or revise business process components to improve results
- Do: Implement the plan and measure its performance
- Check: Assess the measurements and report the results to decision makers
- Act: Decide on changes needed to improve the process
The consolidation phase enables the organization to take stock of what has been taking place and to ensure made to processes that require documentation (both to allow processes to be repeatable and to facilitate recognition of the achievement of some form of quality standard).
Quality standards
The International Organization for Standardization (ISO) created the Quality Management System (QMS) standards in 1987. These were the ISO 9000:1987 series of standards comprising ISO 9001:1987, ISO 9002:1987 and ISO 9003:1987; which were applicable in different types of industries, based on the type of activity or process: designing, production or service delivery. The standards have been regularly reviewed every few years by the International Organization for Standardization. The version in 1994 and was called the ISO 9000:1994 series; comprising of the ISO 9001:1994, 9002:1994 and 9003:1994 versions. The last revision was in the year 2000 and the series was called ISO 9000:2000 series. However the ISO 9002 and 9003 standards were integrated and one single certifiable standard was created under ISO 9001:2000. Since December 2003, ISO 9002 and 9003 standards are not valid, and the organizations previously holding these standards need to do a transition from the old to the new standards. The ISO 9004:2000 document gives guidelines for performance improvement over and above the basic standard (i.e. ISO 9001:2000). This standard provides a measurement framework for improved quality management, similar to and based upon the measurement framework for process assessment.
The Quality Management System standards created by ISO are meant to certify the processes and the system of an organization and not the product or service itself. ISO 9000 standards do not certify the quality of the product or service.
Recently the International Organization released a new standard, ISO 22000, meant for the food industry. This standard covers the values and principles of ISO 9000 and the HACCP standards. It gives one single integrated standard for the food industry and is expected to become more popular in the coming years in such industry.
ISO has a number of standards that support quality management, one group describes processes (including ISO 12207, ISO 15288)and another describes process assessment ISO 15504.
The most elaborated and accepted concept of quality management is the model of the EFQM Excellence Model.
Quality terms
Quality Improvement can be distinguished from Quality Control in that Quality Improvement is the purposeful change of a process to improve the reliability of achieving an outcome. Quality Control is the ongoing effort to maintain the integrity of a process to maintain the reliability of achieving an outcome.
Academic resources
- International Journal of Productivity and Quality Management, ISSN 1746-6474, Inderscience
- International Journal of Quality & Reliability Management, ISSN: 0265-671X, Emerald Publishing Group
See also
- Quality assurance
- Quality audit
- Quality control
- Quality management system
- ISO 15504
- Systems thinking - Applications
- Total Quality Management
- Hoshin Kanri
- Health care
External links
References
- Pyzdek, T, "Quality Engineering Handbook", 2003, ISBN 0824746147
- Godfrey, A. B., "Juran's Quality Handbook", 1999, ISBN 007034003
- Process Assessment and Improvement ISBN 0-387-23182-X