Revision as of 06:27, 6 June 2013 editClueBot NG (talk | contribs)Bots, Pending changes reviewers, Rollbackers6,438,380 editsm Reverting possible vandalism by 2001:630:301:3842:AC30:4439:8726:705 to version by 160.44.230.197. False positive? Report it. Thanks, [[User:ClueBot NG|Cl...← Previous edit | Revision as of 20:31, 22 June 2013 edit undoCmdrObot (talk | contribs)339,230 edits sp: et. al.→et al.Next edit → | ||
Line 1: | Line 1: | ||
] | ] | ||
'''Betz's law''' calculates the maximum power that can be extracted from the wind, independent of the design of a ] in open flow. It was published in 1919, by the German physicist ].<ref>Betz, A. (1966) ''Introduction to the Theory of Flow Machines.'' (D. G. Randall, Trans.) Oxford: Pergamon Press.</ref> The law is derived from the principles of conservation of mass and momentum of the air stream flowing through an idealized "actuator disk" that extracts energy from the wind stream. According to Betz's law, no turbine can capture more than 16/27 (59.3 percent) of the ] in wind. The factor 16/27 (0.593) is known as Betz's coefficient. Practical utility-scale wind turbines achieve at peak 75% to 80% of the Betz limit.<ref name=Enercon/><ref>Tony Burton et |
'''Betz's law''' calculates the maximum power that can be extracted from the wind, independent of the design of a ] in open flow. It was published in 1919, by the German physicist ].<ref>Betz, A. (1966) ''Introduction to the Theory of Flow Machines.'' (D. G. Randall, Trans.) Oxford: Pergamon Press.</ref> The law is derived from the principles of conservation of mass and momentum of the air stream flowing through an idealized "actuator disk" that extracts energy from the wind stream. According to Betz's law, no turbine can capture more than 16/27 (59.3 percent) of the ] in wind. The factor 16/27 (0.593) is known as Betz's coefficient. Practical utility-scale wind turbines achieve at peak 75% to 80% of the Betz limit.<ref name=Enercon/><ref>Tony Burton et al., (ed), ''Wind Energy Handbook'' , John Wiley and Sons 2001 ISBN 0 471 48997 2 page 65</ref> | ||
The Betz limit is based on an open disk actuator; if a ] is used to collect additional wind flow and direct it through the turbine, more energy can be extracted. However, such shrouded turbines are costly to build in utility-scale units because of the extra structure required.<ref>Burton et. al, ''Wind Energy Handbook'', chapter 5 ''Shrouded Turbines''</ref> | The Betz limit is based on an open disk actuator; if a ] is used to collect additional wind flow and direct it through the turbine, more energy can be extracted. However, such shrouded turbines are costly to build in utility-scale units because of the extra structure required.<ref>Burton et. al, ''Wind Energy Handbook'', chapter 5 ''Shrouded Turbines''</ref> |
Revision as of 20:31, 22 June 2013

Betz's law calculates the maximum power that can be extracted from the wind, independent of the design of a wind turbine in open flow. It was published in 1919, by the German physicist Albert Betz. The law is derived from the principles of conservation of mass and momentum of the air stream flowing through an idealized "actuator disk" that extracts energy from the wind stream. According to Betz's law, no turbine can capture more than 16/27 (59.3 percent) of the kinetic energy in wind. The factor 16/27 (0.593) is known as Betz's coefficient. Practical utility-scale wind turbines achieve at peak 75% to 80% of the Betz limit.
The Betz limit is based on an open disk actuator; if a diffuser is used to collect additional wind flow and direct it through the turbine, more energy can be extracted. However, such shrouded turbines are costly to build in utility-scale units because of the extra structure required.
Concepts
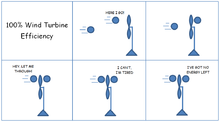
Consider that if all of the energy coming from wind movement into the turbine were extracted as useful energy then the wind speed afterwards would drop to zero. If the wind stopped moving at the exit of the turbine, then no more fresh wind could get in - it would be blocked. In order to keep the wind moving through the turbine there has to be some wind movement, however small, on the other side with a wind speed greater than zero. Betz' law shows that as air flows through area, and when it slows from losing energy to extraction from a turbine, it must spread out to a wider area. Geometry is what limits the turbine efficiency to 59.3%.
Three independent discoveries of the turbine efficiency limit
The British scientist Frederick W. Lanchester derived the same maximum in 1915. The leader of the Russian aerodynamic school, Zhukowsky, also published the same result for an ideal wind turbine in 1920, the same year as Betz did. It is thus an example of Stigler's Law.
Economic relevance
The Betz limit places an upper bound on the annual energy that can be extracted at a site. Even if a hypothetical wind blew consistently for a full year, no more than the Betz limit of the energy contained in that year's wind could be extracted. In practice, the annual capacity factor of a wind site varies around 25% to 60% of the energy that could be generated with constant wind.
Essentially increasing system economic efficiency results from increased production per unit (per windmill square meter of vane exposure or other system component, such as the transmission) Increases in system efficiency which are marginal decreases in cost per kwh are required to bring down the cost of electrical power production. These efficiency increases may or may not be the result of engineering efficiencies that push into the higher levels of the Betz limit. System efficiency increases in power application, transmission or storage may do the same thing at lower cost/unit of power.
Proof
It shows the maximum possible energy — known as the Betz limit — that may be derived by means of an infinitely thin rotor from a fluid flowing at a certain speed.
In order to calculate the maximum theoretical efficiency of a thin rotor (of, for example, a windmill) one imagines it to be replaced by a disc that withdraws energy from the fluid passing through it. At a certain distance behind this disc the fluid that has passed through flows with a reduced velocity.
Assumptions
1. The rotor does not possess a hub, this is an ideal rotor, with an infinite number of blades which have no drag. Any resulting drag would only lower this idealized value.
2. The flow into and out of the rotor is axial. This is a control volume analysis, and to construct a solution the control volume must contain all flow going in and out, failure to account for that flow would violate the conservation equations.
3. The flow is incompressible. Density remains constant, and there is no heat transfer.
Application of conservation of mass (continuity equation)
Applying conservation of mass to this control volume, the mass flow rate (the mass of fluid flowing per unit time) is given by:
where v1 is the speed in the front of the rotor and v2 is the speed downstream of the rotor, and v is the speed at the fluid power device. ρ is the fluid density, and the area of the turbine is given by S. The force exerted on the wind by the rotor may be written as
Power and work
The work done by the force may be written incrementally as
and the power (rate of work done) of the wind is
Now substituting the force F computed above into the power equation will yield the power extracted from the wind:
However, power can be computed another way, by using the kinetic energy. Applying the conservation of energy equation to the control volume yields
Looking back at the continuity equation, a substitution for the mass flow rate yields the following
Both of these expressions for power are completely valid, one was derived by examining the incremental work done and the other by the conservation of energy. Equating these two expressions yields
Examining the two equated expressions yields an interesting result, mainly
or
Therefore, the wind velocity at the rotor may be taken as the average of the upstream and downstream velocities. (This is arguably the most counter-intuitive stage of the derivation of Betz' law.)
Betz' law and coefficient of performance
Returning to the previous expression for power based on kinetic energy:
- .

By differentiating with respect to for a given fluid speed v1 and a given area S one finds the maximum or minimum value for . The result is that reaches maximum value when .
Substituting this value results in:
- .
The power obtainable from a cylinder of fluid with cross sectional area S and velocity v1 is:
- .
The reference power for the betz efficiency calculation is the power in a moving fluid in a cylinder with cross sectional area S and velocity v1:
- .
The "power coefficient" Cp (= P/Pwind) has a maximum value of: Cp.max = 16/27 = 0.593 (or 59.3%; however, coefficients of performance are usually expressed as a decimal, not a percentage).
Modern large wind turbines achieve peak values for Cp in the range of 0.45 to 0.50, about 75% to 85% of the theoretically possible maximum. In high wind speed where the turbine is operating at its rated power the turbine rotates (pitches) its blades to lower Cp to protect itself from damage. The power in the wind increases by a factor of 8 from 12.5 to 25 m/s, so Cp must fall accordingly, getting as low as 0.06 for winds of 25 m/s.
Understanding the Betz results
The Betz results are at first glance a little hard to understand. For example, why is the maximum Betz efficiency 59.3%, when a speed ratio of implies the air passing through the rotor has lost 88.9% of its kinetic energy? The left side of the betz curve shows a maximum efficiency of 50% when the exiting air (V2) has no axial velocity. Is this realistic?
The answer to the second question is easy. 50% efficiency at is not realistic, the model breaks down at very low exit speeds. The Betz model assumes a constant density fluid and that implies the cross sectional area of the flow varies inversely with axial speed. At the cross sectional area is infinite! Mathematically the exiting air does not 'pile up' because it is spreading radially, but radial kinetic energies are not accounted for in the Betz model.
To show that 59.3% Betz efficiency is indeed consistent with a loss of 88.9% of kinetic energy in the air passing through the rotor a physical picture is helpful. The equations for power extracted from the air flow apply to the 'milk bottle' shaped flow shown in the figure at the beginning of this article. The upstream flow (V1) has a cross sectional area less than the rotor area (S). As the flow approaches the rotor, it begins to lose energy, and as it passes through the rotor the equations show it expands to exactly the rotor area (S).
The last step in calculating the Betz efficiency (Cp) is to divide the calculated power extracted from the flow by a reference power value. The Betz analysis uses for its power reference, reasonably, the power of air upstream moving at V1 contained in a cylinder with the cross sectional area of the rotor (S).
The key to understanding why the Betz limit is lower than implied by the speed ratio is to understand that some of the air in the Betz reference cylinder does not pass through the rotor. The area of the flow that will pass through the rotor is upstream smaller than the rotor area. It expands to the rotor area as it reaches the rotor, implying that roughly half the energy transfer from the air to the rotor occurs before passage through the rotor. Thus it must be the case that the air just outside the flow gets pushed radially outward as the rotor is approached just enough so that it bypasses the rotor. The Betz equations do not include any terms for air that bypasses the rotor, its contribution to the extracted power is assumed to be zero.
As a check, let's calculate conditions at the Betz limit: 59.3% efficiency at . The equations show the flow speed at the rotor is the (arithmetic) average of V1 and V2, or . For constant density fluid the product of the speed and area are constant everywhere along the flow, so , where A1 is the area of the flow upstream at V1. Thus A1/S = .666, meaning only 2/3 of the air in the upstream reference cylinder will eventually pass through the rotor and contribute to the extracted power. Thus the denominator in the Betz efficiency calculation is (in effect) inflated by 3/2, so the efficiency based on speed changes (88.9%) must be scaled by inverse of 3/2, or 2/3. gives us the Betz limit. Checks.
The Betz model can also be used to estimate the downstream air speed of real wind turbines. Kinetic energy of wind depends on speed squared, so if a modern large wind turbine is extracting half the wind's energy, which is possible, then from energy considerations it would seem that the downstream air speed (V2) should be x.707 of the upstream air speed (V1). But this is not what the Betz curve shows. Solving the Betz equation for yields with 81% of the air in the upstream reference cylinder actually going through the blade circle, and 19% bypassing the blades due to a radial outward push from the inner expanding air flow as it approaches the blades.
Points of interest
Note that the preceding analysis has no dependence on the geometry, therefore S may take any form provided that the flow travels axially from the entrance to the control volume to the exit, and the control volume has uniform entry and exit velocities. Note that any extraneous effects can only decrease the performance of the turbine since this analysis was idealized to disregard friction. Any non-ideal effects would detract from the energy available in the incoming fluid, lowering the overall efficiencies.
There have been several arguments made about this limit and the effects of nozzles, and there is a distinct difficulty when considering power devices that use more captured area than the area of the rotor. Some manufacturers and inventors have made claims of exceeding the Betz' limit by doing just this; in reality, their initial assumptions are wrong, since they are using a substantially larger
than the size of their rotor, and this skews their efficiency number. In reality, the rotor is just as efficient as it would be without the nozzle or capture device, but by adding such a device you make more power available in the upstream wind from the rotor.Observation: If we use the middle following (harmonic mean) of the speeds
To take the place of
, then if then for whatever value of (impact without motion). The calculation is very simple and gives a 50% output.Modern development
In 1935 H. Glauert derived the expression for turbine efficiency, when the angular component of velocity is taken into account, by applying an energy balance across the rotor plane. Due to the Glauert model, efficiency is below the Betz limit, and asymptotically approaches this limit when the tip speed ratio goes to infinity.
In 2001, Gorban, Gorlov and Silantyev introduced an exactly solvable model (GGS), that considers non-uniform pressure distribution and curvilinear flow across the turbine plane (issues not included in the Betz approach). The GGS model predicts that peak efficiency is achieved when the flow through the turbine is approximately 61% which is very similar to the Betz result of 2/3, but the GGS predicted peak efficiency is much smaller: 30.1%.
Recently, viscous computations based on computational fluid dynamics (CFD) were applied to wind turbine modelling and demonstrated satisfactory agreement with experiment. Computed optimal efficiency is, typically, between the Betz limit and the GGS solution.
References
- Betz, A. (1966) Introduction to the Theory of Flow Machines. (D. G. Randall, Trans.) Oxford: Pergamon Press.
- ^ "Enercon E-family, 330 Kw to 7.5 Mw, Wind Turbine Specification"
- Tony Burton et al., (ed), Wind Energy Handbook , John Wiley and Sons 2001 ISBN 0 471 48997 2 page 65
- Burton et. al, Wind Energy Handbook, chapter 5 Shrouded Turbines
- Gijs A.M. van Kuik, The Lanchester–Betz–Joukowsky Limit, Wind Energ. 2007; 10:289–291
- "Danish Wind Industry Association"
- White, F.M., Fluid Mechanics, 2nd Edition, 1988, McGraw-Hill, Singapore
- Gorban' A.N., Gorlov A.M., Silantyev V.M., Limits of the Turbine Efficiency for Free Fluid Flow, Journal of Energy Resources Technology - December 2001 - Volume 123, Issue 4, pp. 311-317.
- Hartwanger, D., Horvat, A., 3D Modelling of A Wind Turbine Using CFD, NAFEMS UK Conference 2008 "Engineering Simulation: Effective Use and Best Practice", Cheltenham, UK, June 10–11, 2008, Proceedings.
- Ahmed, N.A. & Miyatake, M. A Stand-Alone Hybrid Generation System Combining Solar Photovoltaic and Wind Turbine with Simple Maximum Power Point Tracking Control, IEEE Power Electronics and Motion Control Conference, 2006. IPEMC '06. CES/IEEE 5th International, Volume 1, Aug. 2006 pages 1–7.