This is an old revision of this page, as edited by SmackBot (talk | contribs) at 11:54, 3 February 2008 (Date the maintenance tags or general fixes). The present address (URL) is a permanent link to this revision, which may differ significantly from the current revision.
Revision as of 11:54, 3 February 2008 by SmackBot (talk | contribs) (Date the maintenance tags or general fixes)(diff) ← Previous revision | Latest revision (diff) | Newer revision → (diff)PDCA ("Plan-Do-Check-Act") is an iterative four-step problem-solving process typically used in quality control. It is also known as the Deming Cycle, Shewhart cycle, Deming Wheel, or Plan-Do-Study-Act.
Meaning
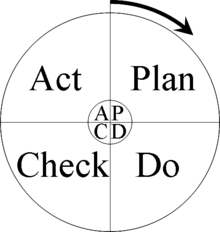
- PLAN
- Establish the objectives and processes necessary to deliver results in accordance with the specifications.
- DO
- Implement the processes.
- CHECK
- Monitor and evaluate the processes and results against objectives and Specifications and report the outcome.
- ACT
- Apply actions to the outcome for necessary improvement. This means reviewing all steps (Plan, Do, Check, Act) and modifying the process to improve it before its next implementation.
About
PDCA was made popular by Dr. W. Edwards Deming, who is considered by many to be the father of modern quality control; however it was always referred to by him as the "Shewhart cycle." Later in Deming's career, he modified PDCA to "Plan, Do, Study, Act" (PDSA) so as to better describe his recommendations.
The concept of PDCA comes out of the Scientific Method, as developed from the work of Francis Bacon (Novum Organum, 1620). The scientific method can be written as "hypothesis" - "experiment" - "evaluation" or Plan, Do, and Check. Shewhart described manufacture under "control" - under statistical control - as a three step process of specification, production, and inspection. Shewhart, 1980, pg. 45. he also specifically related this to the Scientific Method of hypothesis, experiment and evaluation. Shewhart, pg. 48 says that the statistician "must help to change the demand by showing...how to close up the tolerance range and to improve the quality of goods." Clearly, Shewhart intended the analyst to take action based on the conclusions of the evaluation. According to Deming Deming, 1986, pg. 88 during his lectures in Japan in the early 1950's the Japanese participants shortened the steps to the now traditional Plan, Do, Check, Act. Deming preferred Plan, Do, Study, Act because 'Study' has connotations in English closer to Shewhart's intent than "Check." In recognition of this perhaps we should make all references to PDSA, not PDCA.
A fundamental principle of the scientific method and PDSA, is iteration - once an hypothesis is confirmed (or negated), executing the cycle again will extend the knowledge further. Repeating the PDSA cycle can bring us closer to the goal, usually a perfect operation and output.
In Six Sigma programs, the PDSA cycle is called "Define, Measure, Analyze, Improve, Control" (DMAIC). The iterative nature of the cycle must be explicitly added to the DMAIC procedure.
PDSA should be repeatedly implemented in spirals of increasing knowledge of the system that converge on the ultimate goal, each cycle closer than the previous. One can envision an open coil spring, with each loop being one cycle of the Scientific Method - PDSA, and each complete cycle indicating an increase in our knowledge of the system under study. This approach is based on the belief that our knowledge and skills are limited, but improving. Especially at the start of a project, key information may not be known; the PDSA - scientific method - provides feedback to justify our guesses (hypotheses) and increase our knowledge. Rather than enter "analysis paralysis" to get it perfect the first time, it is better to be approximately right than exactly wrong. With the improved knowledge, we may choose to refine or alter the goal (ideal state). Certainly, the PDSA approach can bring us closer to whatever goal we choose.
Rate of change -- rate of improvement— is a key competitive factor in today's world. PDSA allows for major 'jumps' in performance ('breakthroughs' often desired in a Western approach), as well as Kaizen (frequent small improvements associated with an Eastern approach). In the United States a PDSA approach is usually associated with a sizable project involving numerous people's time, and thus managers want to see large 'breakthrough' improvements to justify the effort expended. However, the Scientific Method and PDSA apply to all sorts of projects and improvement activities.
The power of Deming's concept is in its apparent simplicity. The concept of feedback in the Scientific Method (aka inductive logic), in the abstract sense, is today firmly rooted in education. While apparently easy to understand, it is often difficult to accomplish on a on-going basis due to the intellectual difficulty of judging one's proposals (hypotheses) on the basis of measured results. Many people have an emotional fear of being shown "wrong," even by objective measurements. To avoid such comparisons, we may instead cite complacency, distractions, loss of focus, lack of commitment, re-assigned priorities, lack of resources, etc.
Problems with PDCA
![]() | This section possibly contains original research. Please improve it by verifying the claims made and adding inline citations. Statements consisting only of original research should be removed. (January 2008) (Learn how and when to remove this message) |
![]() | The neutrality of this section is disputed. Relevant discussion may be found on the talk page. Please do not remove this message until conditions to do so are met. (January 2008) (Learn how and when to remove this message) |
![]() | An editor has launched a copyright investigation involving this section. The text under investigation is currently hidden from public view, but is accessible in the page history. Please do not remove this notice or restore blanked content until the issue is resolved by an administrator, copyright clerk, or volunteer response agent.
The purported copyright violation copies text from http://www.lc-stars.com/problemswithpdca.html (Copyvios report); as such, this page has been listed on the copyright problems page. Unless the copyright status of the text of this page or section is clarified and determined to be compatible with Misplaced Pages's content license, the problematic text and revisions or the entire page may be deleted one week after the time of its listing. What can I do to resolve the issue?
Steps to list an article at Misplaced Pages:Copyright problems:
|
]
PDCA's application was intended for quality control purposes and proposed continuous improvement in quality of products/experiments. The simple cycle works well in this application, but its simplicity fails in modern complex organizational contexts with the need to engage many people in improvement. The following provides a short overview of shortcomings with PDCA.
First, there is no such thing as continuous quality improvement. By definition, continuous means without interruption. If an enterprise or any part of it is subject to continuous improvement, this implies continuous change. In such a situation people will become rapidly confused about the current status of processes and procedures and/or follow outmoded practices. There is also the real problem of "change fatigue": when people who have to adjust continuously to change (improvement) they become confused, disenchanted or stop following changes. Due to change fatigue, progress tends to grind to a halt within an enterprise. Change requires motivating people, and hence needs to recognize change fatigue and manage it. Change management needs to cover people, process and product. In reality, Shewart and Deming meant Continual Improvement, a cycle of improvement with pauses to consolidate the improvements (changes). These are then subject to checking or study to determine if they have actually improved the area of change. This change from continuous to continual improvement occurred in the ISO standards in the previous release of the standards when it was realized that the wrong terminology was used.
Second, Do and Act have the same meaning in English. Dictionaries provide the following relevant definitions:
- Do • verb 1 perform or carry out (an action). 2 achieve or complete (a specified target). 3 act or progress in a specified way. 4 work on (something) to bring it to a required state.
- Act • verb 1 take action; do something. 2 take effect or have a particular effect. 3 behave in a specified way.
So PDCA could just as easily be PDCD or PACA! In other words: Plan-Do-Check-Do or Plan-Act-Check-Act! This is confusing, and PDCA can thereby seem trivial especially to uninformed personnel. In reality, the real meaning of Act is Improve or Correct! Hence the cycle should read Plan-Do-Check-Improve or Plan-Do-Study-Improve. So the acronym would be PDCI or PDSI!
Third, Shewart assumed that management or experts would act, not the ordinary worker. This is completely outdated thinking in most enterprises today.
Fourth, Plan has a limited range of meaning . It was not intended to cover aspects such as creative or innovative thinking (also called "outside the box" thinking). There are at least 12 modes of thinking, and Plan only covers a couple of these modes of thinking. Many modern quality improvements occur due to creative ideas and innovations, PDCA does not help people to achieve this because it limits the thinking modes.
Fifth, PDCA has an inherent circular paradigm. It assumes that everything starts with Planning. In innovation and invention it is often better not to plan as it can stifle creativity! In addition, it is possible to improve without planning (but not without thought).
Sixth, PDCA was only intended for incremental continual improvement, hence it is not a good methodology for large scale change, especially in large complex organizations.
Therefore, as Deming himself encouraged, we should not just accept what we are told or read, but should learn, understand and intelligently adapt what we learn to suit what we want to achieve, even PDCA!
References
- Shewhart, Walter Andrew (1939). Statistical Method from the Viewpoint of Quality Control. New York: Dover. ISBN 0-486-65232-7.
- Shewhart, Walter Andrew (1980). Economic Control of Quality of Manufactured Product/50th Anniversary Commemorative Issue. American Society for Quality. ISBN 0-87389-076-0.
- Deming, W. Edwards (1986). Out of the Crisis. MIT Center for Advanced Engineering Study. ISBN 0-911379-01-0.
See also
External links
- Note: Before adding your company's link, please read WP:Spam#External link spamming and WP:External links#Links normally to be avoided.